IT'S A STICKY SITUATION
If someone
who knew absolutely nothing about modelbuilding asked you what was the
single most important tool needed for the construction of a kit…besides
the kit, of course, what would you say? A knife? Sprue cutters? Clamps?
Well, they're all important, but you'd be wrong on every count. The most
important tool is the one thing that we really don't think of as a tool.
And what is it? Glue or cement. But even that's not the whole answer because
we don't use just one kind of adhesive today, especially with multimedia
kits being fairly commonplace. Fifty years ago, however, it was a somewhat
different story.
When I started building models back around 1949, most were made of wood.
Anyone out there remember the old stick-and-tissue flying models? They
were powered by a long rubber band that ran the length of the model inside
the fuselage. You wound it up by rotating the prop, then launched the
model into flight by throwing it into the air and removing your finger
from the prop at the same time. Believe it or not, the little puppy actually
flew…and quite well, too.
At
any rate, to join wood parts, we modelers had cement. Two of the best
known were made by Ambroid and Testors and both are still around today.
When styrene plastic took over the model world, new cements reared their
sticky little heads. Testors, as you would expect, came out with their
own version (along with those little ten cent bottles of paint) and another
company that was quickly making a name for itself with plastic kits released
what is arguably the best known and most beloved styrene cement ever produced…Revell
Type 'S'.
For,
I suppose, the next ten years or so (meaning sometime in the early 1960s),
model cements stayed basically the same. Various companies came out with
their own versions, but cement was cement was cement for all practical
purposes. It was also the weak point in model construction. That's because
cement was actually that - cement. Though it would grab the plastic and
hold the parts together, the two parts that were joined were still two
separate parts held together by that layer of cement. Break down an old
model after the cement had dried for a few months -or years- and you could
literally peel a layer of dried cement off the plastic, leaving the smooth
plastic edge behind.
This doesn't mean that plastic (meaning tube) cement didn't work. It
did. I still have models built forty years ago that are as solid today
as they were the day I built them. But things were about to change. Sophistication
would arrive in the form of liquid welders.
Liquid welders have an interesting property in that they literally dissolve
the top layer of plastic, allowing the surfaces of two parts (you have
to hold the two parts together for this to work) to intermingle on a molecular
level, essentially creating a weld, allowing the two parts to become one.
Done correctly, if you try to break the two former pieces apart, one of
the pieces will break somewhere other than the
seam you joined.
Someone discovered this stuff in the retail outlets of commercial plastics
manufacturers of cast acrylic plastic products (also known by the brand
name PlexiGlas). They used a little item called Weld-On #3 to join cut
pieces of acrylic and …lo and behold…it did just as good a job on styrene.
Somebody told somebody who told somebody and the floodgates were opened.
The stuff was water thin and evaporated at a prodigous rate if you left
the cap off and you were working in a hot environment. Wasn't all that
good for your lungs, but somehow we learned safe ways to use it without
killing ourselves in the process. A few of us even went so far as to visit
our local scientific supply house to buy MEK (methyl ethyl ketone) and
MEK-P (methyl ethyl ketone peroxide). Worked just as well, cost less and
was also more dangerous. If nothing else, it proves that modelbuilders
will try just about anything
once if they think it'll work.
Anyway, as liquid welders caught on, more and more manufacturers began
offering them, including Weld-On, Ambroid (they called theirs ProWeld),
Testors, Tenax and many more. Which one you settled on was basically a
matter of personal preference because they all did essentially the same
job. My personal favorite is Ambroid ProWeld. Many of you swear by Tenax
7R while I swear at it. I flat can't make the stuff do what I want it
to because it evaporates too fast, but it works wonders for many. Like
they say, different strokes for different folks.
Finally, let's not overlook the exotics. By this, I mean the cyanoacrylates
and epoxies. Exotic or not, a lot of modelers are now starting to use
CAs (cyanoacrylates or superglues) as their only cement for both building
the basic kit, creating fillets and contours, as well as filling gaps
and imperfections. Now when you're building resin kits or multimedia kits
where you're adding resin and photoetch components to a base styrene kit,
CAs are pretty much your only choice (except for epoxies, which we'll
get to in a minute).
CAs were originally available only in a water thin consistency that
ran literally everywhere. Today, you have water thin, gap filling, slow
cure, slower cure, gel form, even a couple of new flexible versions (one
is rubber toughened and the other is designed as a flexible hinge glue)
from Bob Smith Industries. Other manufacturers you may be familiar with
are Pacer Technologies and Zap Adhesives to mention only a few. You also
have spray-on accelerators to make the stuff kick even faster. Again,
which one you use is a matter of personal preference, though I think Bob
Smith Industries
produces the best line of CAs you can get your hands on.
Incidentally, both Pacer and BSI (Bob Smith Industries) offer accelerators.
Both speed up the cure time of CAs, but there's one very interesting difference
between the two…and this comes from my personal experience. The Pacer
version leaves a very slight residue on the surface after it's dried while
BSI leaves absolutely zero residue. Does this make any real difference
in the construction of a model? Not really, except for one thing. The
BSI version can be used to get a canopy crystal clear. Wear glasses or
an Opti-Visor… or have a scanner for your computer? I haven't found anything
better for cleaning the glass. Sounds weird, I know, but it works.
They cure in seconds, fill gaps that can't be filled any other way,
become rock hard in a short period of time and sand beautifully. I use'em
all the time but, in my humble opinion, they're not a universal product
that can replace every other type of cement, adhesive or welder that you
used to use. In fact, I've yet to see a universal cement adhesive or glue.
They all have their strengths and weaknesses. The trick is to learn what
each product can and can't do, then use the one best suited to your particular
requirements.
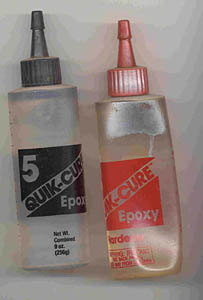 What's
left? Epoxies. These are two part products where you have to mix equal
parts of the two components together before they'll begin to cure. One
more time, there's a wide variety of these little boogers, most of which
you'll find in hardware and automotive supply stores, as well as hobby
shops that cater to radio control modelers. Liquid, semi-liquid, putty
(including Milliput for the modeler), they come in all forms. Some cure
in five minutes, others can take several hours. Some even have a metal
base for use on pipes.
Yep, things have certainly changed in the cement/adhesive/glue area.
Used to be that your choices were real simple. Depending on whether you
were building a wood or plastic model, all you had to do was tell your
father to pick up a tube of Ambroid, Testors or Revell 'S' cement and
you were done. Today you need a catalog to even list all the available
choices, never mind figure out which one will really work best for you.
And keep in mind that I haven't gone near the various specialized woodworker's
glues that are occasionally useful to the plastic modeler.
See y'all next month.
|
|