Revell-Monogram
1/24 scale 2000-2002 NASCAR Monte Carlo
|
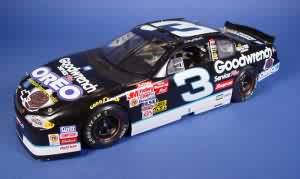 |
Last month we learned how to spruce up one of Revell-Monograms
Dodge Intrepid kits. Based on the Pro-Finish kit platform,
the Dodge has simpler components but turns into a generally accurate
representation of a NASCAR Dodge Intrepid. This month, well learn
how to improve one of the traditional Revell-Monogram full-glue
stock car kits.
The Kit
Monogram introduced its line of full-glue kits in 1983, and its
been one of the most successful lines of kits any manufacturer has produced
to date. Over the years, body shells were updated, and on occasion so
were the chassis, roll cage and engine components. However, while its
fairly simple to tool a new body shell when changes justify it, tooling
a new chassis means essentially tooling a complete new kit. Cost prohibits
doing this with each new body style.
As a result, the builder sometimes has problems with some of these kits.
The full-glue Ford Taurus is a good example. Its chassis was originally
tooled for the mid-1990s series of Ford Thunderbirds. However, in 1998,
when NASCAR let Ford switch to the Taurus, a Taurus body shell was tooled
to fit the T-bird chassis, and additional parts were provided to help
the chassis fit the wider and longer body shell. While this didnt
work too badly, the Taurus nevertheless suffered from ride-height problems
(the body wants to float a bit above the chassis) and wheels/tires
that stick out from the wheel wells (which you fix by grinding away the
plastic disc molded to the inner backing plate/brake drum part).
But while the 1998-1999 Taurus worked reasonably well with the Thunderbird
chassis, the 2000 Taurus body shell simply didnt work well at all.
The roll cage didnt want to sit properly in the body, and nothing
seemed quite right about it. Many NASCAR modelers in the know actually
preferred buying the pre-decorated Pro-Finish kits, stripping them, and
repainting them to use with their favorite decals. (Some of these modelers
say the Pro-Finish body is more accurate, too. Since I was raised in
a staunch Chevrolet household and dont have much interest in any
Ford that wasnt driven by a guy named Fireball, Ill
take their word for it.) Revellogram is due to give us a new Taurus kit
soon, and one hopes itll be based on the Pro-Finish tool.
Why does all this Ford talk matter when the car were about to
build is a Chevrolet? Well, the message is the same. While you wont
have to do Taurus-caliber surgery to the Monte Carlo, youll still
need to do some work to make it look right. Revellograms 2000-2002
Monte Carlo is a good kit, but it needs some work. Among other problems,
its rear spoiler is too small. It also lacks the Earnhardt bar,
that vertical bar running from the dashboard to the roll cage halo. Depending
on the time period youre building a car from, youll need
to work on the front air dam. Youll have lots of work filling gaps
where the front clip and hood meet. The biggest problem with the Monte
Carlo kit is that its chassis has a shorter wheelbase than its body!
If built straight from the box, the front wheels arent centered
in the wheel wells, but sit slightly to the rear.
Construction
I wanted to fix these problems because I have several beautiful out
of production decal sheets for these cars in my collection. Before I
commit a decal sheet to a model, I want to make sure that models
fixed the best I can fix it. For this project well be building
the Goodwrench/Oreo car driven by Dale Earnhardt during the Bud Shootout
at Daytona in February 2001.
Why
this car? Well, I think its probably the best-looking Goodwrench
car Earnhardt ever drove. Maybe Im in the minority, but the usual
black and silver with red-orange striping we associate with Earnhardts Intimidator persona
just looked visually jarring to me. On the other hand, the black and
white with blue striping of the Goodwrench/Oreo car was just
well,
pretty. (Theres also the matter of how good Oreo cookies are, too,
but thats another story.) Its a really good-looking departure
from the usual black cars you see. I fell in love with this car the first
time I saw it, and I knew I wanted to build it.
While
I used a long out-of-production aftermarket decal sheet for this build,
the Revellogram 2001 Earnhardt kit includes Oreo markings on its decal
sheet (along with markings for the standard Goodwrench car he drove in
his final Daytona 500). While the sheet is not quite accurate for either
car (the roofs 3 decal is too small, for one, and there
are some missing decals for both versions), itll let you approximate
the car were building here. (There may be other sheets out there
that will let you build this car, but, not having seen them in person,
I cant comment on them, other to tell you that, from what little
Ive seen on the Internet, some are much better than others.)
Once
more, a disclaimer, if I may: This article isnt about building
the Goodwrench/Oreo car to absolute metaphysical accuracy. Rather, as
with last months, its an exercise in solving some problems.
Youll notice discrepancies between my model and the actual Goodwrench/Oreo
car if you do some research. Once again, my aim is to help you build
some techniques you can apply to your own models. Thank you. You may
now continue
.
THE CHASSIS
The
first modification I made was to stretch the chassis to match the body.
This is simple enough; just cut the frame where the floor pan meets the
chassis rails, then glue some laminated plastic in place until the chassis
is the proper length. Its a subtle stretch, perhaps 3 or 4 millimeters.
Its a good idea to tack-glue the suspension to the chassis, and
fit the chassis and suspension to the body before cutting, so you can
get your own precise measurement. The idea is to center the wheel spindles
in the wheel wells. I made sure the plastic I added didnt stick
below the chassis; that let me use small C clamps to hold a piece of
wood against the bottom of the chassis as it mended. This helped keep
things aligned. Once everything was dry, I could then simply glue .020
sheet to the bottom of the chassis side rails to cover the repair, and
file and sand the other sides of the rails so they were in shape.
Of course, stretching the chassis means you cant use the roll
cage assembly as it came in the kit. As you remember from last month,
I like to build the roll cage separate from the chassis, which gives
me more freedom to paint and detail to my hearts content. Well,
cut the front downtubes off at the firewall and extend them the same
amount you extended the chassis. Some smaller-diameter sections of the
kit sprue are about the correct diameter for this work, so give that
some consideration for stock. I recommend doing this at the firewall
since it means everything is lengthened at the same point and it lets
the kit-supplied tabs and slots up front serve as reference points. One
more thing youll have to do is lengthen the kits driveshaft,
but thats simple enough; just cut a new shaft to fit and glue the
front and rear universal joints to it.
When everything is dry and all the seams are sanded and smoothed over,
you can paint and detail the chassis and engine as you would otherwise.
(Again, my color of choice is Krylon Pewter Gray, over Tamiya spray primer.)
Folks who are so inclined may wish to super-detail these components or
make them appear more prototypically correct; however, Im most
often content to just make kit components look their best. I built the
engine box-stock. The only change I made was to replace the drivers
side exhaust collector with a dual-side exhaust from a Pontiac Grand
Prix kit, as the Oreo car ran with this dual-side collector at Daytona.
ROLL CAGE AND INTERIOR
The roll cage pretty much goes together as advertised. However, I didnt
like the kit-supplied glareshield above the instrument panel, so I made
a new one from .010 styrene. The other addition I made to the roll cage
was the missing Earnhardt bar. This was easy enough to make;
just bend some styrene to the proper angle and glue it in place. I drilled
a hole in the glareshield as a positive locating device. Other things
I did to the roll cage included cutting out the window net and putting
it in the lowered position and adding a small triangular net, made from
strips of masking tape, to the upper right-hand corner of the drivers
side of the roll cage opening.
The seat in the recent Skill Level 3 NASCAR kits has been a source of
pain for many years because its side bolsters are asymmetrical and theres
a head restraint on only one side. While its well-known that Dale
Earnhardt was his own man when it came to seats and safety equipment,
I just made the kits seat symmetrical by adding styrene sheet and
doing lots of cutting and sanding to make each side match up. I added
seat manufacturers logos from a Slixx decal sheet. I also added
a seat belt adorned with Simpson logos in appropriate locations.
THE BODY
The body in these kits is a good start, but there are shortcomings.
There are sunken places in the side panels where the internal mounting/reinforcement
ribs are, and these must be filled and sanded. There are some pretty
gnarly gaps between the hood and the front fenders, notably around the headlight locations.
The rear spoiler is much too small, too.
Theres
one more matter that detail-oriented modelers will want to address. The
Revell-Monogram body portrays a Monte Carlo as approved for the start
of the 2000 NASCAR season. However, effective with the March 2000 Atlanta
race, NASCAR permitted the Chevy teams a slight kickout in the front
air dam. This caused a mild but noticeable change in the cars front
profile. You can represent the modified front air dam with an aftermarket
resin piece (as I did), or you can do it on your own by making vertical
cuts at each corner of the front air dam and up the centerline. This
way you can simply pull the air dam out and forward until youre
happy with the result. Some super glue to fix it, some putty and sanding,
and you have the new front end. (You can also add some sheet plastic
to the bottom of the air dam to make it hug the track a little more,
too.)
Fixing
the rear spoiler is a little more involved. The simplest way would be
to add sheet styrene to both sides and the top, and sand it until its
the proper shape. However, I cut off the spoiler, flipped the body over,
and then began scribing the back corner of the trunk lid with the back
edge of a hobby knife. Eventually the blade broke through that deck edge
where the spoiler had been. I could then cut a new spoiler, in the proper
shape, from sheet styrene. I left a large tab on the bottom of the new
spoiler so I could insert it into the slot Id cut and adjust the
spoilers angle. I got the shape I wanted, but as you can tell,
my angle was slightly off.
No matter, though. It looks much better than the anemic spoiler the kit
supplied.
As
you remember from last month, one area I pay much attention to is where
the hood meets the body. The Monte Carlo needed lots of help here, as
the accompanying photo shows. I installed the hood and taped it in place
from the inside, then used the back of a hobby knife to scribe the separation
lines until they were uniform. When I was satisfied with them, I inserted
strips of sheet styrene into the separation lines and glued them to the
body. Once that dried, I cut down the excess, sanded the joint, and filled
and sanded until the hood and body were trued to my satisfaction.
I
also made one more modification at this point. The Fall 2000 Talladega
race introduced a controversial aero package that included
a roof-mounted taxicab strip and a small lip, called the
Gurney lip, on the rear spoiler. This package was meant to dirty
up the air around each car and lead to more exciting racing, but
things didnt quite work that way (instead, it helped cars clump
up into big packs, led to some pretty spectacular accidents, and may
have played a role in the wreck that killed Earnhardt). This package
was required on all cars in the Daytona and Talladega races in 2001,
but was (thankfully) abandoned before Speedweeks 2002.
I
decided the easiest way to add the taxicab strip would be to scribe a
slot in the roof into which I could later insert a piece of styrene or
brass. As it happened, there was a little break in each of the roof rails
about three-eighths of an inch from the front of the roof. I just aligned
a straight edge with these little gaps and scribed a slot there. I didnt
install the roof strip (or the Gurney lip) until final assembly, as it
would have gotten in the way of finishing the body.
When the bodywork was finished, I primed the body and painted it Testors
Gloss Black from a spray can. (No fancy paint here, folks; just good
ol Testors spray bombs.) I let the body cure for a couple weeks,
then used Micro-Mark sanding pads and Novus Plastic Polish to bring the
body to a very nice shine. This was my first polishing job, and it was
really a revelation to see just what kind of difference it makes in a
car model. After the polish job was done I applied the decals, which
went on with no surprises and really looked gorgeous when they were on
the car.
Mounting
the finished body to the car took some care. I had to trim away the internal
ribs (remember, the ones that caused those nasty sink marks in the sides
of the body) and sand down the top of the roll cage a bit before the
body would sit properly on the chassis. Once I was happy, though, it
was simple enough to glue the body in place. The lengthened wheelbase,
while not exactly perfect, was enough to make a huge difference in how
realistic the model looks.
FINAL DETAILS
Applying
the final details as with any model is where my production
rate really slows down (see last months article). For one thing,
I had to make new side windows, because the Monte Carlo kits windows
feature round ventilation holes instead of the now-standard NACA inlets.
That wont do for my model! I had some NACA inlets that Ralph had
made for me on his Mattel Vac-U-Form, so it was easy enough to cut new
windows from clear sheet, cut out an opening for the duct, and glue the
duct in place. I ran Scale Model Speedway ducting from the rear window
to the oil cooler. At some point I have to make (or buy) a large multi-duct
NACA inlet for the large passengers side door window,
but that will happen in time. I also splurged and installed some Detail
Master hood pins and scuff plates, which look really sharp.
From
here, finishing out the Monte Carlo was much like last months Dodge.
I added the adjustment downtubes, internal bracing, spoiler braces and
overflow tube just as I did on last months model. The bolt heads
between the spoiler braces are nothing more than dots of white glue I
made on wax paper, let dry, painted silver, scraped off and glued in
place. Details specific to this car include the roof strip (made from
sheet brass) and Gurney lip (made from plastic strip) on the rear spoiler,
as well as the side skirts for the exhaust collectors. After a few last
touchups, the model was complete.
Conclusion
Was all this work worth it? Absolutely. Many people flock to diecasts,
but I still prefer to build my own cars, even if they require a lot of
work to make them look correct. Theres a pride of ownership I have
in them, knowing that I did them my way and to my satisfaction. (Thats
not to mention that kits are a lot cheaper than diecast, too, but thats
another story.) There are others to follow from my workbench, too, most
notably Michael Waltrips winning car from the 2001 Daytona 500.
One last note: If youve been reading this article and thinking, Wow,
I could never do that, please let me be the first to tell you that
you can. The first step is to stop telling yourself that you cant
do this level of work. All it takes is practice, and looking at every
model you build as another learning exercise. Ive been building
models pretty much all my life and Im still learning, and each
model I complete is another learning exercise. Above all else, remember
the real reason why we build these things anyway its to
have fun! Build it your way, to your satisfaction, until youre
happy with it.
Now go out there and build something! And have fun! As my Ralph says,
if youre not having fun, you must be doing something wrong.
|
|